Posted in Plasma.
Plasma statt Primer - eine komplett Automation steigert die Effizienz
Written by on .
Von der Aufgabenstellung zur automatisierten Lösung: Plasmabehandlung bei Sita Bauelemente
Plasma statt Primer: Eine Komplett-Automation steigert die Effizienz
Von der Aufgabenstellung zur automatisierten Lösung: Plasmabehandlung bei Sita Bauelemente
Manuelle Arbeit, gesundheitliche Risiken und zeitaufwendige Prozesse – viele Unternehmen stehen vor der Herausforderung, diese Hindernisse zu überwinden. Für Sita Bauelemente, einen Spezialisten für Bau- und Dachentwässerung, haben wir eine Lösung geschaffen, die nicht nur den Workflow revolutioniert, sondern auch die Gesundheit der Mitarbeitenden schützt und neue Möglichkeiten eröffnet.
Die Ausgangslage: Ein klarer Auftrag, komplexe Anforderungen
Sita stand vor der Herausforderung, Kunststoff & Kautschuk Dachbahnen effizient und gleichmäßig zu behandeln, um ihre Haftungseigenschaften zu verbessern. Bislang wurde dieser Schritt durch manuelles Primern durchgeführt – ein arbeitsintensiver Prozess, der gesundheitliche Risiken für die Mitarbeitenden mit sich brachte. Mit Blick auf die Gesundheit der Mitarbeitenden sowie eine effizientere Nutzung ihrer Fähigkeiten entschied sich Sita für eine Automatisierung dieses Arbeitsschritts.
Zielsetzung
- Gesundheitsschutz: Die Mitarbeitenden sollten nicht länger Primer einsetzen müssen, da dies ihre Gesundheit belasten könnte.
- Effizienzsteigerung: Die bisher primernden Mitarbeitenden sollten für andere, produktivere Tätigkeiten eingesetzt werden.
- Qualitätssteigerung: Die neue Lösung musste gleichmäßige und reproduzierbare Ergebnisse liefern, ohne manuelles Eingreifen.
- Integration: Die automatisierte Lösung musste nahtlos in die bestehenden Produktionsprozesse eingebunden werden können.
Unser Ansatz: Partnerschaftliche Entwicklung
Zusammen mit unseren Partnern, der MW-Tec Ingenieurbüro GmbH & Co. KG und der Tigres GmbH, und in enger Zusammenarbeit mit der Sita Bauelemente GmbH haben wir eine Lösung entwickelt, die modernste Plasmatechnologie mit präziser Automatisierung kombiniert.
Prozessablauf: Automatisierte Plasmabehandlung von Kunststoff & Kautschuk Dachbahnen
Der gesamte Ablauf wurde so konzipiert, dass er nahtlos und effizient in die Produktionskette integriert werden kann. Dabei stehen Präzision, Zuverlässigkeit und ein hoher Automatisierungsgrad im Vordergrund. Der Prozess umfasst die folgenden Schritte:
1. Zuführung und Vorbereitung
Die Bauteile, in diesem Fall Dachbahn Abschnitte, werden auf speziellen Rollwagen zur Anlage transportiert. Die Rollwagen werden durch Sicherheitstüren in die Anlage eingeschoben. Dieser Schritt ist vollständig automatisiert und stellt sicher, dass die Bauteile sicher und korrekt positioniert werden.
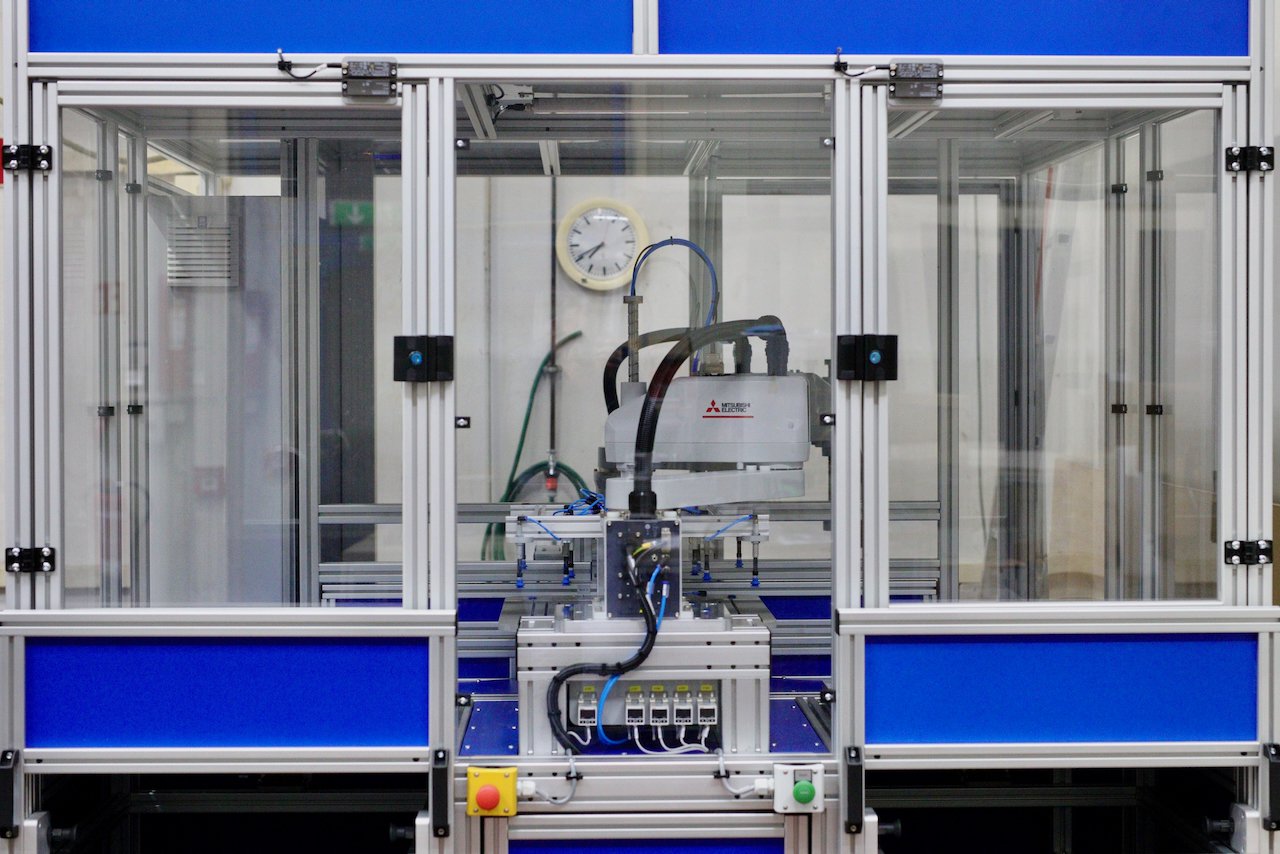
2. Handhabung der Bauteile
Ein Mitsubishi SCARA-Roboter übernimmt das Handling der Dachbahn Abschnitt. Dabei hebt der Roboter die Dachbahn Abschnitt präzise von den Rollwagen ab und positioniert sie auf einem speziell entwickelten Vakuumtisch. Der Vakuumtisch sorgt dafür, dass die Abschnitte während des gesamten Prozesses sicher fixiert sind, ohne dass diese verrutschen.
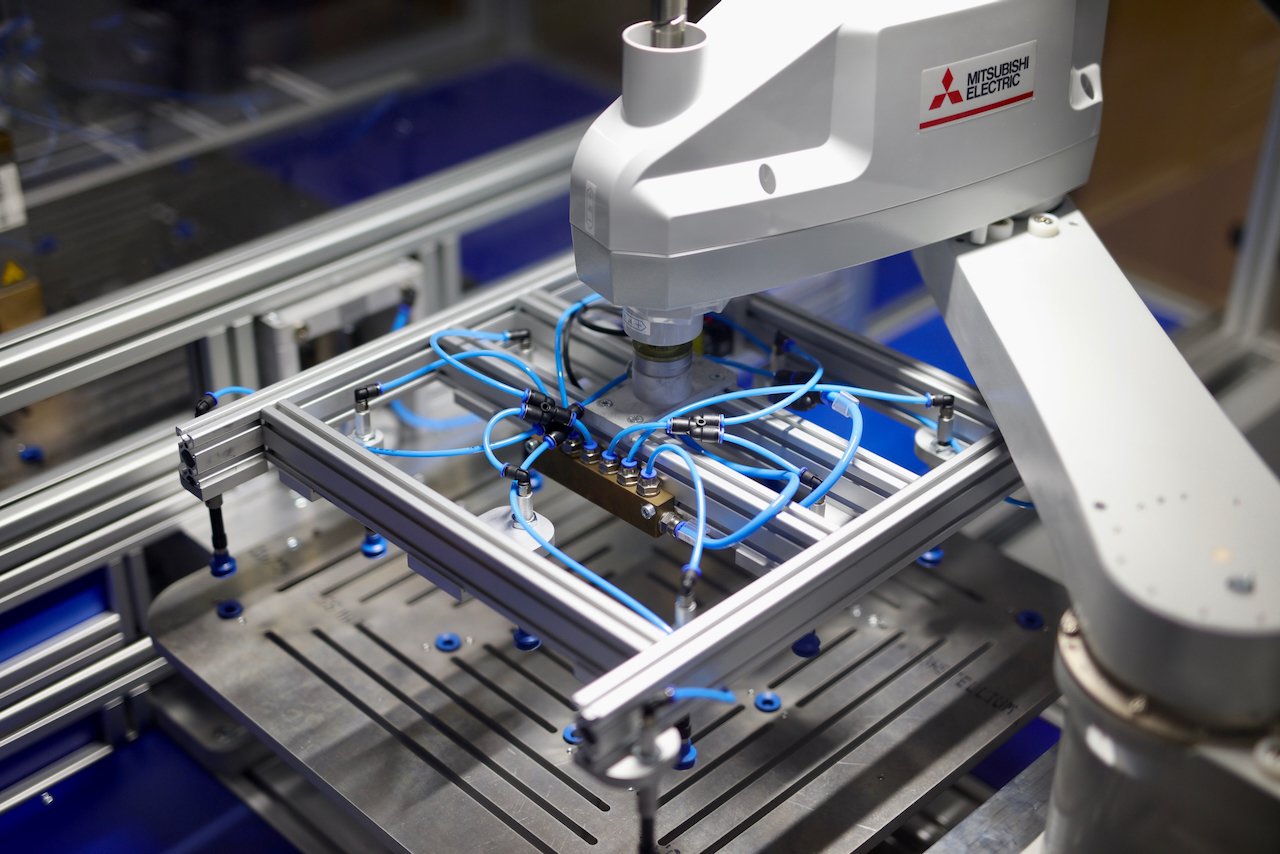
3. Rundschalttisch und Plasmaanwendung
Der Rundschalttisch bewegt die Abschnitte in die optimale Position für die Plasmabehandlung. Eine integrierte Plasmadüse führt dann die Aktivierung der Oberfläche durch. Die präzise Steuerung des Plasmakopfs ermöglicht eine gleichmäßige Behandlung der ausgewählten Kontur auf dem Material, selbst bei komplexen Geometrien. Dieser Schritt wurde durch umfangreiche Testreihen optimiert, um thermische Überlastungen zu vermeiden und die Qualität der Behandlung sicherzustellen.
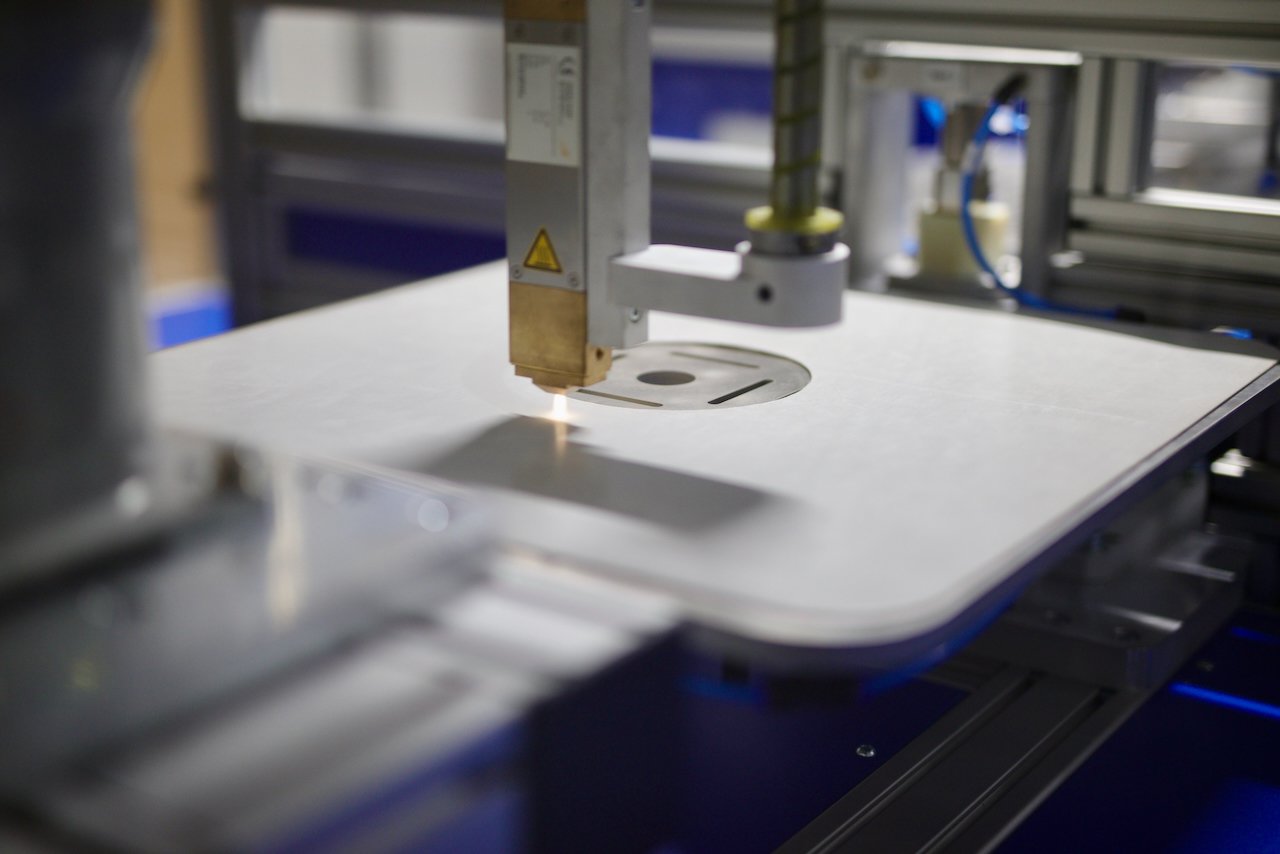
4. Ausschleusung der behandelten Bauteile
Nach der Plasmabehandlung schwenkt der Rundschalttisch zurück in die Ausgangsposition. Der SCARA-Roboter übernimmt erneut und transportiert die behandelten Dachbahn Abschnitt zur Ausschleusung, wo sie für die Weiterverarbeitung bereitgestellt werden.
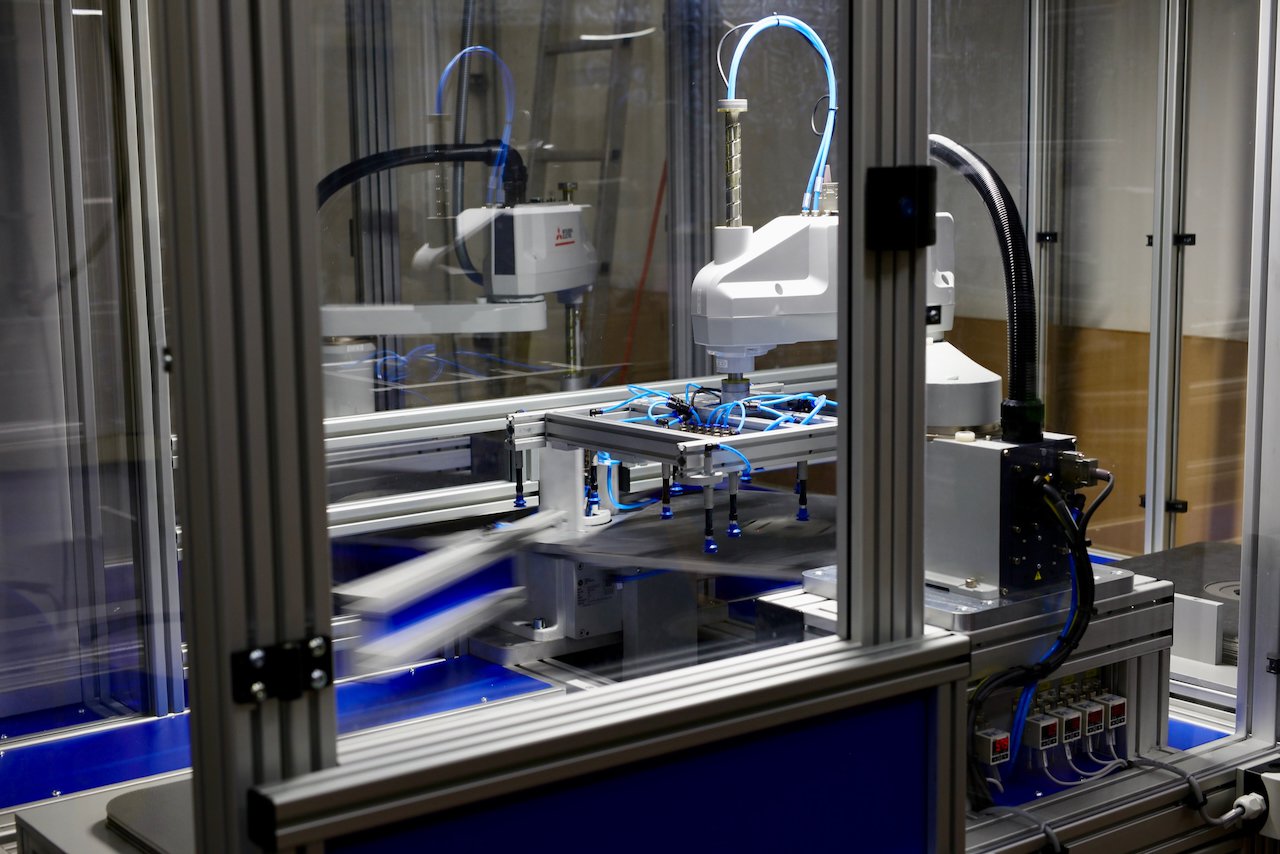
5. Flexibilität und Erweiterbarkeit
Der gesamte Prozess ist modular aufgebaut. Bei einem Produktwechsel kann der Vakuumtisch mit angepassten Saugkreisen, der Roboter mit neuen Greifern und das Behandlungsprogramm entsprechend modifiziert werden. Dies ermöglicht eine hohe Flexibilität und Zukunftssicherheit für wechselnde Anforderungen.
Ergebnisse, die überzeugen
- Steigerung der Effizienz: Die Automatisierung verkürzt die Bearbeitungszeiten erheblich.
- Höhere Qualität: Die Haftungseigenschaften der Dachbahn Abschnitt wurden signifikant verbessert.
- Nachhaltigkeit: Der Wegfall von Chemikalien macht den Prozess umweltfreundlich.
- Bessere Ressourcennutzung: Die Mitarbeitenden konnten von repetitiven Arbeiten befreit und für wertschöpfendere Tätigkeiten eingesetzt werden.
Dank an das Projektteam
Ein solches Projekt wäre ohne die engagierte Arbeit eines Teams besteht aus und und dem Kunden nicht möglich gewesen. Unser besonderer Dank geht an:
- Herrn Christian Behr (Produktmanager)
- Herrn Dominik Boßle (Produktionsleiter)
Fazit: Eine Erfolgsgeschichte für Sita Bauelemente
Dieses Projekt zeigt, wie technisches Know-how, Innovationsgeist und Hartnäckigkeit zu einer Lösung führen, die Kundenanforderungen übertrifft. Die realisierte Plasmabehandlungsanlage setzt neue Maßstäbe in der Oberflächenvorbereitung und zeigt eindrucksvoll, wie aus einer Idee eine voll funktionsfähige, zukunftssichere Lösung wird.
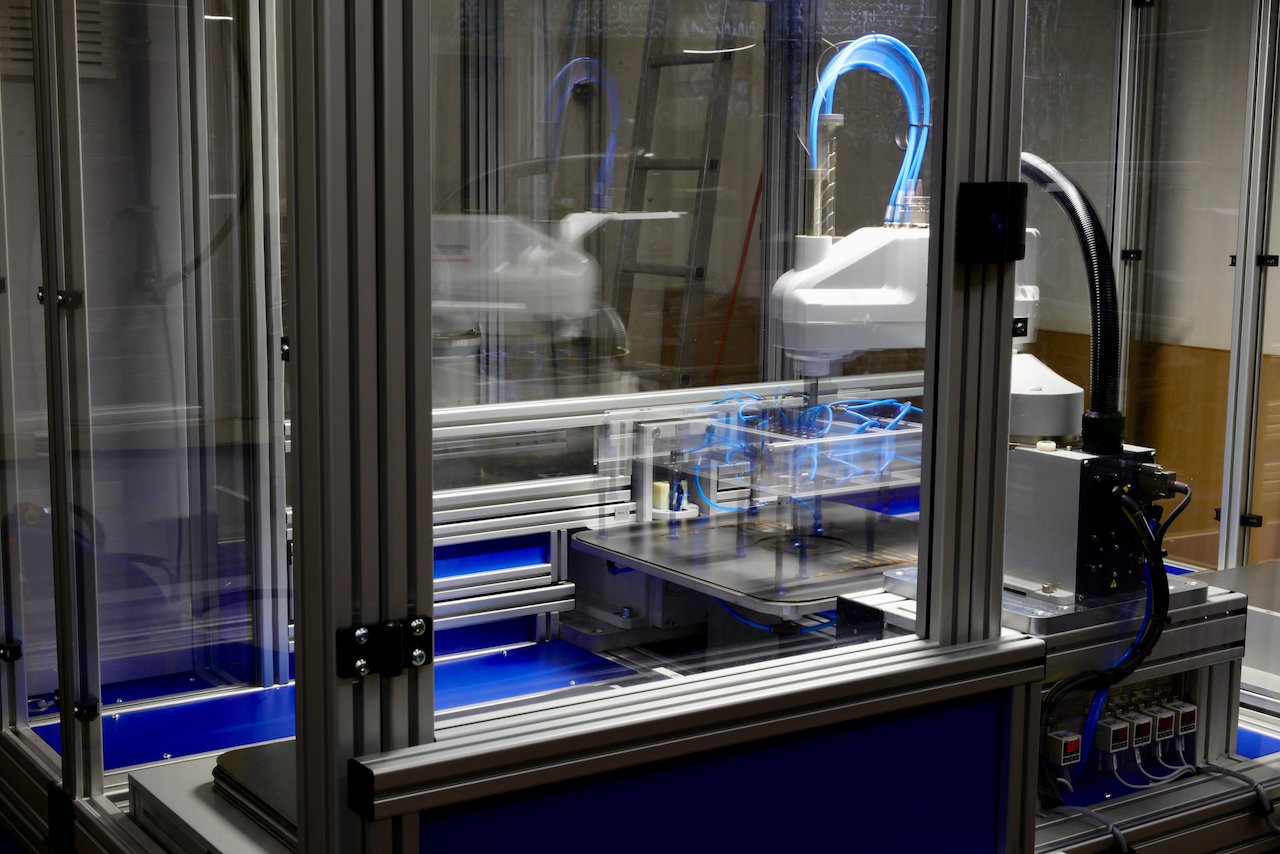
Video-Einblicke
Sehen Sie die Anlage in Aktion: